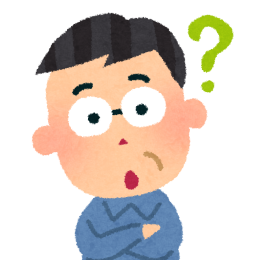
「オーディオは見た目が全てだ!」
という意見があるが、ワテも大体そう思う。
さて、以前に自作したラッチングリレー式スピーカーセレクターのシャーシを新しく作り直すことにした。
そのスピーカーセレクターの製作記事はこちら⤵
このスピーカーセレクターの特徴としては、以下の通り。
- 1 in 5 out(1台のアンプ出力を5台のスピーカーで切り替えて鳴らせる)
- 5連のモーメンタリ型プッシュボタンスイッチで切り替える
- ラッチングリレーを採用したので切替時のみリレーコイルに通電する
- モノラル2台構成(左右独立のシャーシ)
などか。
このスピーカーセレクターのシャーシはMDFボードで即席で作ったので今ひとつ見た目が良くない。
そこで今回、新しいシャーシを自作して中身を入れ替える事にしたのだ。
完成写真を以下に示す。
写真 新型シャーシに入れ替えたラッチリレー式スピーカーセレクター(モノラル2台構成)
では、本題に入ろう。
現在のシャーシ
下写真に現在のシャーシを示す。
写真 MDFボードで自作したシャーシの見た目が安っぽい(改造前)
ダイソーで売っている6ミリ厚のMDFボード(300x600x6t)は200円と安いのでワテはDIYでよく使う。
そのMDFボードをカットして木工用ボンドで貼れば色んなDIY作品を作れるのでお勧めだ。
写真 モノラル2台構成ラッチングリレー式スピーカーセレクターシステム(改造前)
電源はDC12Vのアダプターを使う。
このスピーカーセレクターシステムは上写真のように一方のシャーシのフロントパネルに5連のモーメンタリ型プッシュボタンを付けていて、それを押すと押した番号のスピーカーが選択される。
左右のユニットは下写真に示すLANケーブルで接続して連動するようにしている。
写真 モノラル2台構成ラッチングリレー式スピーカーセレクターシステム(改造前)
スピーカー切り替えはラッチングリレー(=ラッチリレー)を使っている。
ラッチングリレーとは、回路を切り替えるときだけ数十ミリ秒程度のパルス信号をコイルに流せば良いのだ。上写真で使ったPanasonicのラッチングリレーはセットコイルとリセットコイルが独立している2コイル型だ。
一方、セットコイル、リセットコイルが一体になっている1コイル型もあるが、ワテの場合は2コイル型のほうが分かりやすいので2コイル型を好んで使っている。
オーディオマニアはなぜ端子台を使わないのか?
ワテ自作のスピーカーセレクターは上写真に示すように、接続には端子台を使っている。
パワーアンプの出力端子に端子台を使っているオーディオ製品は最近は見ないだろう。
通常は下写真のようなスピーカー端子(左)にバナナプラグ(中央)やY型プラグ(右)が使われる。
![]() ![]() |
![]() ![]() |
![]() ![]() |
スピーカー端子 | バナナプラグ | Y型プラグ |
表 一般的な金メッキ端子類
オーディオマニアな人はこの部分には金メッキ端子が必須だと思っている人が多いだろう。
もし非金メッキな鉄素材なんて使うと、接点が酸化して音が劣化するので絶対に良い音が出ないと主張するに違いない。
と言うワテも昔はそんな気分になっていたので、金メッキ端子崇拝者の気持ちは分からないではないが。
しかし良く考えていただきたい。
金メッキだろうがなんだろうが、電気的な接続部分にバナナプラグを差し込んで接続するなんてのは信頼性が求められる場所では絶対に採用されない接続方法だ。
通常は端子台にY型や丸型の圧着端子をネジ固定するのが一般的だし、電気機器、工場、その他、色んな場所で端子台は使われている。
最高レベルの信頼性が要求される原子力発電所の中なんて端子台が無数に使われているし。
逆にそんな場所でバナナプラグを差し込むような危なっかしい接続方法が使われるとは思えないし。
と言う事で端子台に丸型圧着端子を強固にネジ止めする方法は手軽だし電気的にも最も確実な部類の接続方法なのだ。
それ以上の信頼性を求めるなら、はんだ付けあるいは溶接してしまうと言う案もあるが、接続を変更する箇所ではそれはあまり実用的ではないし。
という訳でワテはオーディオ機器に端子台をよく使う。圧着端子はY型だと抜け落ちる可能性があるのでワテは専ら丸型圧着端子を使う。
新しいシャーシの製作
金メッキ端子類は使わないワテであるがオーディオは見た目が重要だ。
心地よい音楽を聴くとドーパミンやエンドルフィンという物質が脳内に分泌されるらしいが、オーディオもまさにそれと同じだろう。
金メッキを見ると脳内ドーパミンの分泌が促進されるなら、それも悪くはない。
ワテの場合は見栄えが悪いMDFボード製のスピーカーセレクターシャーシを見栄え良く作り直すことで脳内ドーパミンを増やすのだ。
サイドウッドの製作
新型シャーシはサイドウッドを自作して、アルミ複合板の底板にサイドウッドを固定して組み上げることにした。
下写真のように欅(ケヤキ)素材でサイドウッドを作ることにした。
この欅板は以前に一枚300円くらいで売っていたので、何かに使おうと思って買ってみたのだ。
写真 左:欅板、右:サザンレッド材
大体の寸法は以下の通り。
サザンレッド 45 x 286 x 12 mm
欅板は買った時には真っ直ぐだったが、二年弱ほど乾燥させていたら下写真のようにかなり歪んでいる。
写真 欅板(左)は板目なので乾燥させたらかなり反っている
そこで上写真右のサザンレッドという木材をホームセンターで買ってきて、欅板に貼り付けて欅板の歪みを矯正することにした。
下写真のようにタイトボンド3を刷毛で塗る。
写真 タイトボンドは刷毛で塗ると塗りやすい
タイトボンド3で貼り合わせた欅板とサザンレッド材は下写真のようにBesseyのクランプでしっかりと固定して乾燥させる。
写真 貼り合わせた欅板とサザンレッド材をBesseyクランプで固定
このベッセイのパラレルクランプは部材をしっかりと平行に固定出来るのでDIYで活躍する。
翌朝確認したら、歪んでいた欅板は真っ直ぐに矯正されていた。大成功だ!
接着が完了したので、四枚の側板を仕上げサンダーで研磨しておいた(下写真)。
写真 接着が完了した四枚の側板を仕上げサンダーで研磨するためにクランプ
L型クランプは木工DIYだけでなく金属加工でも活躍する。
写真 接着が完了した四枚の側板を仕上げサンダーで研磨する
このマキタの仕上サンダーはリサイクル屋でかなり安く売っていたので買ってみた。
中古なのだが見た目は新品同様で、なぜか知らないが物凄く安かったのでラッキーだった。
表面研磨した欅板にクルミオイルを塗る。
写真 仕上げサンダーで磨いた欅板の美しい木目
下写真のように食用クルミオイルを塗布した欅板は木目が鮮やかに浮き上がる。
写真 食用クルミオイルを塗布した欅板は木目が鮮やかに浮き上がる
下写真がクルミオイルを塗り込み完了した欅板だ。
写真 クルミオイル仕上げのサイドウッドが完成
欅関連商品
写真 サイドウッド内側に貼り付けたサザンレッド
と言う事で、欅板を使ったサイドウッドはいい感じで完成した。
シリコンシーラントで底板をサイドウッドに貼り付ける(失敗)
アルミ複合板はいつもはA4サイズ(210x297x3t)を使うのだが、今回使う欅板が長さ297mmしか無いので、これだとフロントパネルやリアパネルを取り付ける余裕が無い。
いつもはサイドウッド材は長さ307mm程度のものを使っている。
なのでA4サイズのアルミ複合板を287mmくらいにカットして使う事にした。
卓上スライド丸のこの刃をオールマイティ刃に交換した。
写真 アルミ複合板3ミリ厚を卓上スライド丸のこでカットする(切断前)
サイドウッドとアルミ複合板底板を貼り合わせる。
いつもはセメダイン 超多用途接着剤 スーパーX クリアかボンド GPクリヤーを使って張り合わせるのだが、今回はシリコンシーラントを使ってみた。
下写真のように瓶に入れて保管しているシリコンシーラントをサイドウッドのサザンレッド材に塗った。
写真 セメダイン シリコーンシーラント クリアでサイドウッドとアルミ複合板を貼る
下写真のようにアルミ複合板を貼り付けてクランプ固定した。
写真 シリコンシーラントでサイドウッドとアルミ複合板を貼り合わせている様子
この状態で一晩乾かした。
シリコンシーラントはアルミ複合板の接合には適さなかった
今回採用したシリコンシーラントはアルミ複合板の接着には全く適さなかった。
下写真のようにアルミ複合板がペリッと簡単に剥がれてしまった。
写真 アルミ複合板がペリッと剥がれてシリコンシーラントがサイドウッドに残っている
シリコンシーラントは木材同士の接合には適しているが、アルミ複合板には全く適さないようだ。
失敗は成功の元だ。
下写真のように金属製ヘラでサイドウッドに付いているシリコンシーラントを剥がす。
写真 金属製ヘラでサイドウッドに付いているシリコンシーラントを剥がす
なぜワテがシリコンシーラントを使ったのかと言うと、下記事で示すフロアスイパーを以前に自作した時にシリコンシーラントで木材を貼り合わせた。
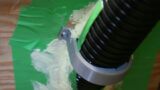
そのフロアスイパーを先日解体したのだが、シリコンシーラントで木材同士が物凄く強固にくっついていて解体するのに苦労したのだ。
バールを使って数時間掛かりで解体出来たが、その時の経験でシリコンシーラントは強力な接着剤としても使えるかな!?と思ったので今回試しに使ったのだが、失敗だった。
あとで気がついたのだが、下写真のようにアルミ複合板の表面に貼ってある保護シートを剥がしていなかった。
この透明シートは恐らくポリエチレンなどの素材だと思うが、ポリエチレンは接着材が付きにくい素材だ。
なので、透明シートを剥がしてから再びシリコンシーラントを試そうかなと思ったのだが、中止した。
再び失敗する可能性も高いので。
写真 アルミ複合板の表面には保護フィルムが貼ってあった
そこで、次は2液混合型のエポキシ系接着剤で貼ってみたのだが、それも失敗した。
具体的には有名なアラルダイトで底板をサイドウッドに貼り付けたのだが、一晩乾かして力を加えたら、またしてもペリッと簡単に剥がれてしまった。
ボンドGPクリアーで底板をサイドウッドに貼り付ける(失敗)
シリコンシーラント、アラルダイトは失敗に終わったので、いつも使っているボンドGPクリアーを使ってサイドウッドとアルミ複合板底板を貼り合わせる事にした。
最初からそうしておけば良かった。
写真 いつも使っているボンドGPクリアーでサイドウッドとアルミ複合板底板を貼り合わせ
下写真のようにクランプして一晩乾燥させた。
写真 ボンドGPクリアーでサイドウッドとアルミ複合板底板を貼り合わせ中
ところが、翌朝チェックしてみたらサイドウッドと底板は簡単に剥がれてしまった。
う~ん、訳分からん。
恐らく最初に使ったシリコンシーラントが木材部分に染み込んでいてそれが接着剤を弾いているような感じだ。
皿ネジで底板をサイドウッドに貼り付ける(成功)
三回連続で接着に失敗したワテであるが、それにも挫けずに作業を進める。
皿ネジで固定することにした。
写真 底板をサイドウッドに固定するのに使ったタッピング皿ネジ(3×12)
下穴を開けたあとで、下写真のようにインパクトドライバーで皿ネジをねじ込んだ。
写真 インパクトドライバーで皿ネジをねじ込む
アルミ複合板は柔らかいのでインパクトドライバーで強くネジをねじ込むとネジ頭がめり込んでしまう。
なので、最後の締めはインパクトドライバーではなくて、手動のプラスドライバーを使った。
左右各4個、合計8個の皿ネジで固定した結果、アルミ複合板底板とサイドウッドはしっかりと固定出来た。
今後は類似のサイドウッドシャーシを自作する場合には、接着剤は使わずに上写真のように皿ネジで組み立てる予定だ。
確実だし、短時間で完了するので。
フロントパネルをMDFボードで作る
フロントパネルは本当はアルミ板などで作る予定だったのだが、適当なアルミ板が手持ちに無かったので、手持ちに有った6ミリ厚のMDFボードでフロントパネルを作ることにした。
写真 ダイソー6mm厚のMDFボードでフロントパネルを作る
フロントパネルには5連のプッシュボタンスイッチとその上にΦ2の赤色LEDを取り付ける穴を開ける必要がある。
解体した旧シャーシもMDFボードでフロントパネルを作っていたので、その穴位置を下写真のように新シャーシのパネルに鉛筆で書き写した。
写真 旧パネルに開けた穴位置を新パネルに写し取る
その穴位置にΦ9ミリとΦ2ミリの穴を各5個ずつ開けた。
写真 ボール盤にΦ2ミリの鉄工ドリルを付けて穴開け作業中
スターエム竹用ドリルは木工作業の穴開けに最適だ。「竹用」というのは木材よりも硬い竹にも穴開けが出来ると言う意味なので、竹用ドリルは木材にも使える。
竹用ドリルで開けた穴はバリが殆ど出ないので、木工作品の仕上がりが綺麗になるのだ。
フロントパネルは黒のつや消し塗装をしておいた。
写真 フロントパネルは黒のつや消し塗装をした
MDFボードは塗料を吸い込むので、合計4回くらい重ね塗りした。
それでもまだ塗料が染み込む感じだ。
なので、塗装面が今ひとつ綺麗に仕上がらなかった。
とりあえず今回はこのMDFボードパネルを使うが、将来、アルミ板などで作り替えても良いかな。
新しいシャーシにスピーカーセレクター基板を移植する
さて、新しいシャーシがほぼ完成したので、スピーカーセレクターの基板を移植する。
旧シャーシをカットする
ところがその移植作業が一筋縄では行かないのだ。
その理由は下写真の10個のラッチリレーは上面に両面テープを貼って上下をひっくり返してMDFボード底板に貼り付けているが、それを剥がすと配線がバラけるかも知れないのでややこしい。
写真 10個のラッチリレーは両面テープでMDFボード底板に貼り付けている
そこでリレーはMDFボードから剥がさずに余白を切り取ることにした。
写真 旧シャーシに10個のラッチリレーを貼り付けたままMDFをカット
上写真のように10個のラッチリレーをMDFボードに貼り付けたまま余分なMDFを卓上スライド丸のこでカットした。
それと、上写真の旧シャーシのスピーカーセレクターは端子台がシャーシ側面に付いている。
新シャーシでは端子台はシャーシ後方に向けたいので、旧MDFシャーシ底板の幅を狭くする必要があるので大きくカットしたのだ。
新シャーシにスピーカーセレクター基板を移植
旧シャーシのMDF底板を小さくカット出来たので、新シャーシ底板に両面テープを貼って基板を移植する。
写真 新シャーシの底板に旧シャーシの部品一式を移植して貼り付ける
下写真のように無事に移植に成功した。
写真 旧シャーシの中身を無事に新シャーシに移植に成功した
ちなみに「移植」繋がりで言うと、ワテは上顎の親知らずを下顎に移植して、被せ物の土台として使って虫歯治療して今のところ順調だ。
親知らずを安易に抜歯する人が多いが、ワテは一本も抜いていない。いや一本抜いたが、再利用している。
なお、端子台と10個のリレーはΦ0.9mmの銅単線をはんだ付けして接続しているが、その部分は全部のはんだ付けを外して端子台を180度回転させてから再はんだ付けしている。
その理由は、端子台の形状が片側からしか圧着端子を入れられないタイプなので、端子台位置を側面から奥側に変更するに当たり、端子台を180度回転させる必要性が生じたから。
ハンダ除去作業では、数ヶ月前に購入したこのハンダ除去機が活躍した。
と言うか、半田吸い取り網線などで作業するのは非常に効率も悪いし、込み入った場所の半田吸い取りは網線ではやり辛い。
なので電動ポンプ式の半田吸い取り機は電子工作をやるなら必須と言っても良いだろう。
と言うワテも長い電子工作人生でほんの数ヶ月前に買ったのだが。
もっと早く買っておけば良かったw
ゴム足を貼る
オーディオ機器は脚に使うインシュレーターで音が変わるらしい。
なぜならオーディオ機器の有名ブランドDENONさんのサイトに以下の説明がある。
インシュレーターの素材や種類について
振動を抑える働きをするインシュレーターですが、インシュレーター自体の素材や形状が音質に影響するとも言われています。
インシュレーターの素材には、金属、木材、ゴム、樹脂、それらを組み合わせたハイブリッドタイプなどもあり、素材によって音の傾向が異なります。一般に木製のものは暖かみがあり、金属製のものはクリアだと言われます。
引用元 https://blog.denon.com/6625/
放送局用オーデオ機器を開発しているデンオンさんが言うのだから間違いないだろう。
でもまあワテの場合は、予算の関係で最も安い部類のゴム足を採用した。
剥がすとシールになっているので貼り付けるだけの手軽さだ。
写真 タカチの薄型のゴム足をシャーシ底板四隅に貼り付ける
フロントパネルを新シャーシに接着する
MDFボードで作成したフロントパネルを接着剤でサイドウッドに貼り付けた。
写真 MDFボードで作成したフロントパネル(黒つや消し塗装済)
接着剤はGPクリアーを使った。
写真 接着剤(GPクリアー)でフロントパネルを貼る
下写真のようにサイドウッドの内側のサザンレッド材にもGPクリアーを塗布した。
写真 サイドウッドの内側のサザンレッド材にもGPクリアーを塗布した
このあと、フロントパネルを貼り付けた。
なおGPクリアーなどのゴム系の接着剤は完全硬化するのではなくて、固まってもゴム状になるので柔らかい。
必要なら剥がしてしまうことも出来るし、剥がした跡に残る接着剤もゴム状なので剥ぎ取る事も可能だ。
要するにやり直したり、改造がやり易いのでDIYにはお勧めだ。
ただし、ゴム系の接着剤は強度的には弱いし、発熱するパワーアンプのシャーシをGPクリアーで張り合わせると熱で接着が剥がれる事もあるので要注意だ。その時はネジ固定などが良いだろう。
5連プッシュボタンとLEDをフロントパネルに固定する
フロントパネルに下写真の5連プッシュボタン(モーメンタリ)とLED表示部が一体となったアルミLアングルを貼り付ける。
写真 5連プッシュボタン(モーメンタリ)とLED表示部をフロントパネルに貼り付ける
この場合も両面テープで貼り付けた。
このニトムズ製の両面テープもワテはDIYでよく使う。
難接着材料のポリプロピレンやポリエチレンにも良く付くので汎用性が高いのだ。
下写真のようにいい感じで貼り付け出来た。
写真 フロントパネル裏側の様子(LED電流制限抵抗は空中配線だ)
上写真で赤色LEDは先端部がΦ2mmなのでMDFボードにも鉄工ドリルでΦ2穴を開けている。
その結果、上写真のように差し込むだけで摩擦でいい感じにLEDが保持されている。
もし緩い場合には裏側からホッドボンドで固定する予定であった。旧シャーシではLEDをホッドボンドで固定していた。
ワテもダイソーで買ったグルーガンを持っているのだが、安かろう悪かろうという感じでホットボンドの出が悪くスムーズに出ないのだ。ドバーッと出たり出なかったりと。
なので、1000円くらい出してもう少し良さそうなグルーガンを買いたいと思っている。
新シャーシに移植したラッチリレー式スピーカーセレクター(モノラル2台構成)
と言う事で、無事に新シャーシにスピーカーセレクター制御基板類を移植することが出来た。
以下では完成した新シャーシのスピーカーセレクターを写真で紹介しよう。
写真 スピーカーセレクター(5連プッシュボタンスイッチ付)
DC12Vリレーを使ったので電源はDC12VのACアダプターを使う。
ラッチリレー制御に使っているSN74xxロジックIC駆動に必要な5Vはこの12Vから三端子レギュレータで生成している。
下写真のように2台のスピーカーセレクターはストレートタイプのLANケーブルで接続する。
写真 ストレートタイプLANケーブル(写真オレンジ色)で接続
LANケーブルを使っているがLANのプロトコルで通信するのではなくて、プッシュボタンを押下した時に発生するパルス信号を伝送する目的に使っている。
それと、12V, 5V, GNDもLANケーブルで伝送している。
注意事項としては必ずストレートタイプのLANケーブルを使うこと。
もしクロスケーブルを使うと電源ON直後の数秒でSN74xxロジックICがぶっ壊れるので要注意だ。
下写真のように欅のサイドウッドが美しい。
写真 欅の木目が美しいサイドウッド
下写真のように天板も3mm厚のアルミ複合板を付ける。接着せずに嵌め込んでいるだけだ。
写真 天板を外せば端子台に簡単にアクセスできる構造
上写真のように天板を外せば端子台に簡単にアクセス出来るので、オーディオラックに設置した場合でも裏に回らなくてもスピーカー配線の変更が可能なのだ。
完璧な設計だ!
左右2台に分けたモノラル構成なので、それぞれのスピーカーセレクターを左右のスピーカー付近に設置すれば各スピーカーまで最短のケーブルで接続出来る。そしてスピーカーセレクターとパワーアンプは紅白のスピーカーケーブル1本で配線するだけで良いので非常にスッキリと配線出来る。
この点も完璧な設計だ!
と言う事で下写真のように2台モノラル構成のラッチングリレー式スピーカーセレクターを新シャーシ移植が完了した。
写真 新シャーシ移植が完了したラッチングリレー式スピーカーセレクター
ラッチングリレーは回路を切り替えるときだけコイルに通電する。
白色プッシュボタンを押すと小気味よく「カチッ」という音を立ててリレーが切り替わる。
いい感じだ。
まとめ
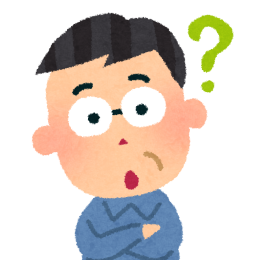
サイドウッドとアルミ複合板底板との接着で数回の失敗をしたが、無事に新シャーシに移植することが出来た。
当記事ではワテが数年前に自作したラッチングリレー式スピーカーセレクター(モノラル2台構成)を新型シャーシに移植した作業過程を紹介した。
従来の旧型シャーシはMDFボードを貼り合わせただけの安っぽい外観だったが、今回は高級欅板にクルミオイル仕上げでサイドウッドを自作したので高級感あるシャーシが完成したと思う。
製作費用の概算は以下の通り。
材料 | 単価 | 数量 | 小計 | 説明 |
欅板 | 300 | 4 | 1200 | 51 x 297 x 13 mm |
サザンレッド | 150 | 4 | 600 | 45 x 286 x 12 mm |
アルミ複合板 | 30 | 4 | 120 | A4(210x297x3t) |
接着剤 | 少々 | GPクリアーなど | ||
クルミオイル(GABAN)1L | 少々 | |||
ステンレスタッピング皿ネジ 3×12 | 10 | 16 | 160 | |
合計 | 2080 | シャーシ2台分 |
表 シャーシ2台の製作費用概算
上表のようにシャーシ1台を約千円で製作出来たので、プアオーディオ派のお財布には優しいぞ。
ちなみにA4サイズのアルミ複合板が一枚30円は安すぎるがこれは以前にヤフオクで100枚セットで3000円で売っているのを買ったのがまだ沢山残っているから。
もし皆さんがアルミ複合板を買うならホームセンターで3×6サイズ(910mm×1820mm 厚さ3mm)を数千円で買ってカットして貰えばA4サイズ一枚あたり400~500円くらいで入手出来ると思う。
タカチ製作所さんのサイドウッドシャーシは製造中止になってしまったので、もし皆さんもサイドウッドシャーシを自作したいならワテのやり方を参考にすれば案外簡単にサイドウッドシャーシを自作出来るだろう。
ワテの場合はラッチングリレーが好きだ。
普通のリレーだと回路の状態を保持するために、コイルにはずっと通電している必要がある。それは電気の無駄遣いでしょ。数百ミリワット程度だとは思うが、塵も積もれば山となるのだ。
世界中のリレーをラッチングリレーに変更すれば原発何基分かの電力を節約出来ると思うのだが。
ラッチングリレーをオーディオ機器に使えば、音楽信号が流れているリレー接点近くにあるコイルは通電していないので、音楽信号に対してコイル電流で発生する電場や磁場の影響は無いだろう。
一方普通のリレーならコイルは常に通電しているので音楽信号にも影響を与えそうだし。
世間のオーディオ機器に使われているリレーの多くは恐らく普通のDCリレーだと思うのだが、高級オーディオ機器ならラッチングリレーを採用すべきだと思う。
と言う事で今後の予定としては、この新型シャーシに作り替えたスピーカーセレクターをワテのプアオーディオ機器に組み込みたい。
それとは別に、リモコン制御出来るスピーカーセレクターを自作したいと考えている。
当記事で紹介したスピーカーセレクターはSN74xxシリーズのロジックICだけで作ったのだが、リモコン制御となるとそれもロジックICだけで実現するのはワテの技術力では難しい。
なのでArduinoやAVRマイコンを使ってリモコン式ラッチングリレースピーカーセレクターを自作したいと考えている。
(続く)
リモコン式(試作機)を作ってみた。
リモコン式(完成版)
コメント