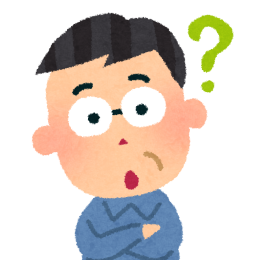
DIYでは紙やすりや金工ヤスリなどで材料を研磨・研削する作業が多い。
その時に出る粉塵は体にも悪いし掃除も面倒だ。
当記事では、ワテが最近自作した表題の「サイクロン集塵機能付き研磨作業台」の製作過程とその使い方を紹介したい。
低予算で中々使いやすい良い作品が完成したので気分爽快だ。
では本題に入ろう。
サイクロン集塵機能付き研磨作業台の製作
まずは下写真に完成した「サイクロン集塵機能付き研磨作業台」を示す。
写真 完成した「サイクロン集塵機能付き研磨作業台」で鉋台の平面出し作業の様子
上写真ではワテが長年使っている寸四鉋の鉋台の下端を削っている様子を示す。
その時に発生する粉塵をサイクロン集塵装置で吸引している。
粉塵は作業台に開いている多数の小穴を通して洗濯ホースに吸い込まれるのだ。
ホームセンターに行けば有孔ボード(穴あきベニヤ板などとも言う)を売っているが、ワテはダイソーで200円で買った300x400x5tのデザインボードというやつを使った。
写真 ダイソー200円の300x400x5tのデザインボードを使う
この有孔ボードは研磨作業をしていると表面に傷も付くと思うので、消耗品と考えて安い材料を採用した。シナベニア製の有孔ボードだとこのサイズでも千円くらいするので勿体ない。
下写真は底板に使う塗装コンパネをワテ自作の丸ノコカット作業台で長方形に切り出している様子を示す。
写真 塗装コンパネの端材を自作丸ノコカット作業台でカット中
上写真のワテ自作作業台は奥と右端にアルミ角パイプを直角に固定している。それらを基準にして、板材を丸ノコで精度良く直線カット出来るのだ。
かつ、洗濯ホースを利用した集塵ホースを接続していて自作サイクロン集塵システムで吸引している。丸ノコの電源コードも洗濯ホースと共にメッシュのケーブルカバーで一体化しているので作業性が良い。
メッシュケーブルカバーは編組スリーブ、編組チューブなどとも言う。
アマゾンで編組チューブを見る。
下写真のように三辺を直角に切り落とした。このあと、残りの一辺もカットして長方形の板が完成した。
写真 塗装コンパネの端を自作丸ノコカット作業台でカットした
次は、有孔ボードを額縁のように支える側板の加工だ。
厚さ5ミリの有孔ボードを額縁のようにはめ込む為に、下写真のように自作トリマーテーブルを使って側板に深さ5ミリの加工を施した。
写真 有孔ボードをはめ込む段差をトリマーテーブルを使って加工した
下写真がその拡大だ。
写真 有孔ボードをはめ込む段差をトリマーテーブルを使って加工(拡大)
このあと、鑿(ノミ)を使って細部を加工して下写真のように有孔ボードをはめ込めるように組み上げた。
写真 有孔ボードを額縁のように嵌め込んだ
当初は単なる木枠を作って、それに有孔ボードをタイトボンドで貼り付けたのだが、ダイソーの有孔ボードはタイトボンドが乾燥すると簡単に剥がれてしまったのだ。
そこで計画変更して、木枠をこのように額縁枠のように段差加工をして有孔ボードをはめ込む構造にした。
その結果、有孔ボードを交換出来るし、有孔ボードを外せば簡単に内部も清掃出来るので一石二鳥と言う感じ。
下写真は裏側から撮影したものだ。
写真 裏側から撮影
下写真のように塗装コンパネの台座に額縁枠を固定した。
写真 塗装コンパネの台座に額縁枠を固定した
額縁枠の高さは約38mmだ。
底板の塗装コンパネが有孔ボードよりも広い理由は、必要なら塗装コンパネ部分をクランプ固定出来るようにするためだ。
そうすれば力いっぱい研磨しても研磨作業台が動くことが無い。
これで研磨作業台は完成した。
あとは、サイクロン集塵機を接続出来るように集塵ポートを付ける作業だ。
3Dプリンタで集塵ポートを印刷する
Fusion 360と言う高性能な3D CADが無料で使える時代なのだから、DIYをやる人は使わな損だぞ。
自称3Dデザイナーのワテであるが、三十分程度で下写真のようなホース継ぎ手を設計出来た。
写真 ワテ設計の集塵ホース接続用の継ぎ手
下写真は裏側から見たものだ。
写真 ワテ設計の集塵ホース接続用の継ぎ手(裏側)
どう!完璧なデザインでしょ。
大きな楕円形の開口部から徐々に円形の集塵ポートに変化する形状もFusion 360を使えば簡単にデザイン出来るのだ。
Fusion 360でデザインが完了したらSTLファイル形式で出力して、フリーなスライサーソフトCuraで読み込む。
そのCuraでgcodeファイルに出力すれば3D印刷の準備完了だ。
gcodeファイルをSDメモリカードに入れて、下写真の3DプリンタのSDスロットに挿す。
写真 3D印刷成功した集塵継ぎ手
下写真のように6時間45分掛かった。
写真 印刷には6時間45分掛かった
下写真は印刷した継ぎ手と集塵濯ホースだ。
写真 印刷した継ぎ手と集塵濯ホース
早速挿し込んでみた(下写真)。
写真 洗濯ホースを自作継ぎ手に挿し込んだ
上写真のように、いい感じでピッタリと刺さっているのが分かるだろう。
素晴らしい。
ちなみにワテが使っている3Dプリンターは熱溶解積層法(ねつようかいせきそうほう、fused deposition modeling、FDM)のタイプだ。要するにリールに巻いてあるフィラメントと呼ばれる樹脂素材を熱で溶かしながら積み重ねて目的とする形状にするのだ。
3Dプリンターは色んな種類のものがあるが、一般にはこのFDM方式か光造形方式がよく使われている。
印刷した継ぎ手は下写真のように取り付ける予定だ。
写真 印刷した継ぎ手の取り付け位置
印刷した継ぎ手を取り付ける作業
木枠に楕円形の穴を開ける
さっそくこの継ぎ手を先程作成した木製木枠の側面に取り付ける。
その為には木枠に楕円形の穴を開ける必要がある。
下写真のように透明テープを貼って楕円開口部の輪郭を赤マジックで写し取った。
写真 透明テープに楕円開口部の輪郭を赤マジックで写し取った
その透明テープを下写真のように貼り付けて、この部分に穴を開ければ良い。
写真 透明テープを木枠に貼り付けてこの部分に穴を開ける
で、早速Φ24ミリの木工ドリル刃を電動ドリルに付けて穴を開けた。
写真 穴あけ作業をするためにバリ防止の下板をクランプ固定
で、下写真のように穴あけしたら、コーススレッドでドリル刃がガリガリ。あかんがな。
写真 コーススレッドに気づかずにドリル穴あけしてしまった
まあ、人生失敗もある。そう言うもんや。
と気を落ち着かせるワテであるが、一週間くらい気になるだろう。
Φ24ミリのドリルはガリガリやってしまったので、コーススレッドを抜いて再び穴あけした。
その結果、ガリガリして多少は刃先に傷が付いているけれども、穴あけ能力はそれほど低下していないようで、問題なく穴を開ける事が出来た。
写真 Φ24、Φ18などのドリルを使って楕円形内部に穴あけ加工した直後
その後、Φ24、Φ18などの手持ちのドリル刃を幾つか使って楕円形内部に穴あけ加工した。
上写真のように大量の切屑が出たが、サイクロン集塵装置を使えば下写真のように一瞬で綺麗に吸い取れるのだ。
写真 サイクロン集塵装置は木工DIYには必須と言っても良い
ワテ自作のサイクロン集塵システムの記事はこちら⤵️
外丸鑿を使って楕円形に加工する
下写真の外丸鑿は昨年の三木金物まつりで1000円で買ったやつだ。
写真 外丸鑿を使って楕円形に加工する
一本1000円と安かったので買ったのだが、早速活躍する時が来た。
下写真のように外丸鑿を使って楕円形に切り出す。
写真 外丸鑿はこう言う作業で役立つ
ちなみに上写真の大型金槌も三木金物まつりで買ったやつだ。
下写真のように楕円形に切り出せたので、最後に鏝鑿(コテノミ)を使って切断面をさらに綺麗に加工した。
写真 鏝鑿(コテノミ)が活躍する場面
上写真のように鏝鑿を使うと普通の鑿では作業し辛い状況でも、やり易い。
この鏝鑿も三木金物まつりで千円で買ったやつだ。
ワテの大工道具はセール品、中古品が多い。
DIY界のSDGs派と呼ばれているワテである。
で、兎に角、下写真のように側板の米松材(厚さ15mm)に楕円穴を開ける事が出来た。
写真 側板の米松材(厚さ15mm)に楕円穴を開ける事が出来た
3D印刷した集塵継ぎ手の表面を研磨する
熱堆積法の3Dプリンタで印刷した物体はフィラメントの最初と最後の繋ぎ目でスムーズに繋がらずに盛り上がりが生じる(下写真)。
写真 継ぎ手の側面に直線状に膨らみがある
この直線状の膨らみを120番手の紙やすりで研磨した(下写真)。
写真 継ぎ手側面の直線状の膨らみを120番手の紙やすりで研磨した
こう言うちょっとした研磨作業で出る粉塵が煩わしいのだ。
今ワテが作っている研磨作業台こそ、こう言う状況で使いたいのだ。
下写真のように継ぎ手を側板にクランプ固定しておいて、ナベネジ3.5×16を4個使って固定した。
写真 継ぎ手を側板にナベネジ3.5×16を4個使って固定
下写真が完成形だ。
写真 3D印刷した継ぎ手を取り付けた研磨作業台(完成形)
サイクロン集塵しながら研磨作業台を使ってみる
では、完成した研磨作業台を早速使ってみる。
下写真のように、「鉋台 砥石の面直し器」を使って鉋台の下端を削る。
写真 完成した研磨作業台で「鉋台 砥石の面直し器」を使って鉋台の下端を削る
この「鉋台 砥石の面直し器」も中古で買ったやつだ。確か千円くらいだった。
下写真のようにワテが長年使っている寸四鉋の台をゴシゴシと擦る。
写真 ワテが長年使っている寸四鉋の台をゴシゴシと擦る
上写真では静止画なので分かり辛いが、白樫の台をゴシゴシと研磨すると発生する粉塵の多くは有孔ボードに吸い込まれるので、それほどは周囲には飛散しない。
とは言っても、研磨作業台には有孔ボードの穴が沢山開いているので、手が吸い付くほど強い吸引力は無い。
研磨作業が終わったら、紙やすり表面に残っている木くずをトントンと叩き落とした(下写真)。
写真 紙やすりに残っている粉塵を軽く叩き落とした
上写真のように吸引力はそれ程強く無いので、多くの粉塵は作業台の上に残ったままだ。
でもその粉塵を下写真のようにダスター刷毛で掃いて有孔ボードの穴に落としてやればサイクロンが吸ってくれるのだ。
写真 ダスター刷毛で研磨作業台の上の粉塵を掃く
その結果、下写真のように研磨作業台上の粉塵は綺麗に吸い取られるのだ。
写真 ダスター刷毛を使うと簡単に清掃出来る
と言う事で、下写真のように研磨作業台の上に散らばっていた削りカスは綺麗にサイクロン掃除機が吸ってくれるのだ。素晴らしいぞ。
写真 作業終了したらダスター刷毛を使って作業台を清掃
なお、有孔ボードを外してみると下写真のように格子状に粉塵が積もっている。
写真 塗装コンパネの上に格子状に粉塵がある
この格子状の粉塵もダスター刷毛で掃いて集塵ポートの辺りに持っていけば、サイクロンが吸ってくれる。
写真 塗装コンパネをダスター刷毛で掃いて清掃
ダスター刷毛は何気ないツールであるが、DIYやる人は数本買っておくと便利だぞ。
ワテの場合は作業台の前に一つ、ボール盤に一つを釘に引っ掛けて常設している。
作業中にちょっとした清掃に使えるので、お勧めだ。
今回の作業でも、穴あけ加工に使った木工ドリル刃をダスター刷毛で清掃してから収納した。
そう言う作業習慣を付けておくと、作業環境をいつも清潔かつ整理整頓した状態に保てるのだ。気分も良いし。
と言う事で、今回製作したサイクロン集塵ポート付の研磨作業台は、ワテの描いていた通りの使いやすい良い作品が出来た。
寸四鉋のメンテナンスの様子
下写真の寸四鉋(土牛太郎)はもう何年も前から使っているやつだ。
写真 メンテナンス中の寸四鉋(土牛太郎)の現在の様子
上写真のように鉋台は上端、下端、両側面をRYOBI手押し鉋盤で削ったあと、表面を研磨して白樫の綺麗な表面が出ている。
鉋刃や裏金も真鍮ブラシで擦って錆を落とした。鉋刃の頭が金槌で叩いて潰れている部分は金工ヤスリで軽く削っている。
ちなみに、メンテナンス前の寸四鉋(土牛太郎)の様子を下写真に示す。
写真 メンテナンス前の寸四鉋(土牛太郎)の様子
上写真の古びた鉋も、ちょっと手を加えるだけでこんなに綺麗になるのだ。
写真 古びた鉋もちょっと手を加えるだけでこんなに綺麗になる
この寸四鉋(土牛太郎)は刃先の角度が22度くらいだった。
ワテが長年、適当に研いでいたのでドンドンと刃先が鋭角になったようだ。
一般に鉋の刃先角度は28度くらいが良いらしい。
兵庫県三木市の有名な鉋鍛冶の会社である株式会社常三郎さんのサイトから引用させていただく。
鉋の刃の角度は約28°~30°が良いとされています。
角度が鋭角になれば刃コボレの原因になり、鈍角になれば引きが重くなります。 しかし、削る材質に応じて角度を調整すれば、切れ味が良くなります。 柔木を少し鋭角に(桐勾配は約21°)、堅木は鈍角(約33°~35°)が一般的です。
ワテの寸四鉋は刃先角度が22度くらいだったので、卓上グラインダーで削って26度くらいまで削って鈍角にした。グラインダー作業では刃先が高温になると焼入れ状態が変わる恐れがあるので、一気に削らずにじっくり時間を掛けて少しずつ削った。
写真 刃先角度を26度くらいに荒削りした状態
![]() |
![]() |
写真 左:メンテナンス前、右:メンテナンス中
下写真のように、ワテの古い寸四鉋(土牛太郎)は見た目はわりと綺麗になったのだ。
写真 古い寸四鉋(土牛太郎)は見た目はわりと綺麗になった
調整前は鉋刃を台に手で強く押し込んでも刃先が刃口から1cm以上引っ込んでいた。
それを金槌で叩いて刃口に刃を出していたので、台にかなり無理な力が掛かっていた。それ以上きついと台が割れていた可能性もある。
そこで、刃を支えている左右の溝の部分を細い角ヤスリを使って削って左右にそれぞれ0.5ミリくらいの隙間が出来るくらいに広げた。
そして、再び刃を手で台に押し込んだのが下写真で、刃先が刃口から3ミリくらい奥の位置に来ている。これならあとは金槌で軽く叩けば刃口から刃先が出るので台に無理な力も掛からないはずだ。
写真 古い寸四鉋(土牛太郎)の下端や刃口の様子
今後の予定としては、砥石を使って刃先を研ぎ上げる作業と、鉋台の下端を平坦に削ったので、あとは台直し鉋を使って下端を3点支持に調整したい。
台直しに関しても常三郎さんのサイトから引用させていただく。
台の調整
中仕上げの下端調整は、台頭(二分)、刃口(一分)、台尻(二分)の3点を残し、台直し鉋でペーパー1枚分を削り落とします。仕上げは刃口(五厘)、台尻(一分)を残して仕上るのが基本。
台がひねったり、内マルになった場合は、プレーナーか台直しペーパーで平らに加工してから調整してください。
ちなみに鉋台の下端調整は3点支持や2点支持など幾つかの手法があるので、どっちが良いのかはワテは知らない。その辺りも今後学習したいと思っている。
まとめ
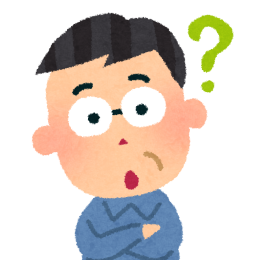
安い費用で良い作品が完成すると気分が良い。
当記事では「サイクロン集塵機能付き研磨作業台」を自作する過程とその使い勝手を紹介した。
材料費は数百円くらい。
ワテは3Dプリンターで継ぎ手を印刷したが、3Dプリンターを持っていない人は何らかのフランジ付きの継手を流用するか、あるいは水道用の塩ビパイプを側板に穴あけして接着するなどの工夫をすれば良いだろう。
完成した「サイクロン集塵機能付き研磨作業台」を実際に使ってみて、ワテ所有の寸四鉋の台を研磨する作業をやってみた。
その結果、研磨作業中の粉塵の飛散もある程度は抑える事が出来るようになり、かつ、作業中にダスター刷毛を使って掃除すればサイクロン集塵機が粉塵を吸い取ってくれるので、研磨作業が格段にやり易くなった。
今回のDIYは大成功と言っても良いだろう。
簡単に作れるので皆さんにもお勧めしたい。
なお、卓上グラインダーで作業する場合にも粉塵が飛び散る。今回作成した研磨作業台の上に重い卓上グラインダーを載せるのは無理があるので、何らかの補強をするなどの改造を検討中だ。
取り敢えずワテ所有のRYOBIミニ卓上グラインダーならこの研磨作業台の上には乗せられる重さなので、今度試して見る予定だ。
(続く)
コメント