
ワレコ
春になったと思ったら「今年初の30度超え真夏日を岩手県で観測」なんてニュースをやっているぞ。
まだ四月末だと言うのにもう夏なのか?
暑さに弱いワテである。
さて塩ビ管スピーカー自作プロジェクトであるが、2022/3/31にPCBWayさんに発注していた3Dプリントパーツが無事に到着した。
CADデータをPCBWayさんのサイトにアップロードして約二週間で自宅に到着した。
以下に示す前回記事ではそのCADデータ作成過程とPCBWayさんへの発注作業のやり方を解説している。
当記事では、その3Dプリントパーツの紹介とそれらのパーツを塩ビ管に取り付ける為に塩ビ管に穴開け加工を行ったので、その作業過程を紹介したい。
3Dプリンタは数万円程度から購入できるので小物なら自分で印刷する事も可能だ。
今回の印刷物はかなり大き目なのと、合計八点の印刷物が必要になるのでPCBWayさんに発注したのだ。
3Dモデルを自分で描けば、手軽に発注出来るのでお勧めだ。
では本題に入ろう。
PCBWayさんから届いた光造形法による3Dプリントパーツ
ワテの場合、PCBWayさんに3Dプリントを発注するのはこれで二回目だ。
前回(第一回目)は、ABS素材を使って熱溶解積層法(FDM、Fused Deposition Modeling)で発注した。その時に製作して貰ったのは自作キュービックスピーカー用のスピーカーターミナルの台座だ。
今回は光造形法(SLA、Stereolithography Apparatus)による3Dプリントを発注したのだ。
下写真はPCBWayさんから届いた小包を開封した様子を示す。運送業者さんはFedexを指定した。
![]() |
![]() |
![]() |
写真 PCBWayさんから届いた光造形法3Dプリントパーツ一式
上写真のように各パーツは個別に厳重にクッション材で包まれている。
下写真が今回発注していた3Dプリントパーツ一式だ。
写真 PCBWayさんから届いた光造形法による3Dプリントパーツ一式(八点)
上写真のパーツを見たワテの第一印象としては、今回の光造形法による3D印刷物は非常に精度良く出来上がっていて、まさにこんなパーツを期待していたんだ!と言う驚きと感動だ。
PCBWayさんにアップロードした3Dモデルの通りに細部まで綺麗に印刷されているのだ。
手で触った感じでも重量感があり十分に硬いので強度的にも全く問題無い。
スピーカー固定台座
さっそくこれらのパーツを塩ビパイプにあてがってみた(下写真)。
写真 塩ビ管(呼び径150)VU150x500mm外側にピッタリはまるスピーカー台座
おお、塩ビ管の曲面にピッタリと合っているぞ!
次に、塩ビパイプ内側に取り付けるパーツもあててみた(下写真)。
写真 塩ビ管(呼び径150)VU150x500mm内側ピッタリはまるスピーカー台座固定パーツ
いや~、素晴らしい。
自分で熱溶解積層法方式の3Dプリンタで印刷しても、ここまで綺麗に印刷するのは難しい。実際、今回試しに自分の3Dプリンタで少し印刷してみたのだが、最も大きなパーツなら印刷時間が1日以上掛かるのだ。そんな長時間印刷して成功するかどうか分からない。
それも合計八個ものパーツを印刷する必要がある。そこでPCBWayさんに発注したのだ。
光造形方式の3Dプリンタの長所をネット検索してヒットしたページを引用させて頂く。
造形スピードが速く生産力が高い
1個造形する場合と複数造形する場合で造形時間が変わらないため、3Dプリンターの造形方式の中でも、生産能力の高い方式であると言えます。造形精度が高い
光造形方式では、光硬化性樹脂を使用するため、熱溶解積層方式(FDM方式)などのように材料が高温にならず、熱収縮を起こしにくいです。そのため、寸法などの精度が高い造形物を造形することができます。滑らかな仕上がり
積層痕が目立ちにくく、表面が滑らかな仕上がりになるのも光造形方式の特徴の一つです。積層していく際に、硬化する層と一つ前に硬化された層がしっかりと結合するため、層と層の境目が目立ちにくいのです。同様の理由から、面による耐久性の差もほとんどありません。
引用元 https://3dprinter.co.jp/3404/#lwptoc6
下写真のようにこれら二種類のパーツを組み合わせて塩ビパイプにスピーカーを固定するのだ。
写真 スピーカー固定台座用パーツが塩ビパイプにピッタリと合っている様子
おお、設計通りにパーツが仕上がっているので、上写真のようにピッタリ合うのだ。
ある種の快感がある。
スピーカーターミナル取り付け台座
下写真はスピーカーターミナルを取り付ける台座だ。
写真 スピーカーターミナルを取り付ける台座
上写真のようにこちらの台座も塩ビパイプの曲面に隙間なくフィットしている。
この台座には下写真のように白色レジストで製作したプリント基板を固定するのだ。
写真 スピーカーターミナル固定台座とPCBWay製白色レジスト基板
上写真のプリント基板には下写真のように三種類のコネクタを取り付ける予定だ。
写真 以前に作成したキュービックスピーカーの接続端子
上写真のように、バナナプラグ、スピコン、圧着端子(丸型、Y型)の三通りの接続方法が可能なスピーカーターミナルなのだ。
その製作記事はこちら↴
光造形法と熱溶解積層法の3Dプリント作品を比較
下写真左の白色パーツが今回PCBWayさんで光造形法で製作して貰った3Dプリント作品(Resin素材)だ。一方、右側の黒色パーツは以前に同じくPCBWayさんで製作して貰った熱溶解積層法による3Dプリント作品(ABS素材)だ。
写真 3Dプリント作品比較 白色:光造形法(Resin素材)、黒色:熱溶解積層法(ABS素材)、ともにPCBWay製
黒色の作品はABS樹脂製なので強度もあり粘りも有る感じ。表面には堆積されたフィラメントの筋が見える。
一方白色のレジン素材を使った光造形法による作品は、表面は滑らかでエッジ部分や穴形状も綺麗に仕上がっているのが分かるだろう。ただしレジン素材はABS樹脂に比べると若干弱い感じがする。
なお、PCBWayさんの3D印刷サービスにはこれらの素材以外にも多数の素材が選べる。金属素材も選べるのだ。金属素材で3D印刷出来るなんて、ワテには想像つかないハイテクな世界だ。
写真 3Dプリント作品の細部の比較 白色:光造形法(Resin素材)、黒色:熱溶解積層法(ABS素材)、ともにPCBWay製
光造形法と熱溶解積層法のどちらを選ぶかは、目的とする作品の用途に応じて決めると良いだろう。
今回はABS樹脂ほどの強度は必要無く、どちらかと言えば微細な構造も正確に印刷出来るとネットで評判の高い光造形法を選択してみたのだ。Resin素材で印刷された白色パーツは、手で触った感じでは十分に硬くて強度も有る感じ。
もし今後、何かの3D印刷を再びPCBWayさんに依頼する場合には、ワテとしては光造形法を選びたい。
PCBWayさんの光造形法による3Dプリント費用
今回の光造形法で製作した作品の費用は以下の通り。
スピーカー固定台座 約30ドル/個
当然ながら、印刷物のサイズが大きくなると費用が増える。
前回、ABS素材で熱溶解積層法で印刷して貰った黒色パーツも一個当たり数十ドル程度の費用だった。
今回、合計8点の印刷に掛かった費用総額は以下の通り。
Fedex送料 US $ 42.88
割引 -US $ 3.97
合計 US $ 171.25
Fedexの送料が約42ドルなので、いつものプリント基板の時の送料(約20ドル)よりも掛かってしまった。その理由はたぶん小包のサイズと重量が大きくなったからだろう。
3Dプリント台座にFOSTEXスピーカーを嵌めてみる
下写真のFOSTEXスピーカーを使う。
写真 今回使うFOSTEX P1000Kフルレンジ 10cm スピーカーユニット
このスピーカーを下写真のように台座に固定するのだ。
写真 FOSTEXスピーカーユニットを3D印刷台座に載せてみた。いい感じ。
上写真では四カ所のネジ穴位置もピッタリと合っている。
ワテがFusion360を使って設計した通りに出来上がっているぞ!
スピーカー固定台座は下写真のように塩ビパイプに取り付ける予定だ。
写真 マスキングテープを使ってスピーカー固定台座を仮固定してみた
上から見ても、二つのパーツが塩ビパイプにピッタリとフィットしている(下写真)。
写真 スピーカー固定台座は設計通りの仕上がり
と言う事で、PCBWayさんに発注していたスピーカー固定台座は、ワテの設計通りにいい感じに出来上がっている。
写真 スピーカー固定台座、プリント基板固定台座
スピーカーの固定にはM4ネジを使う。ナット側は下写真の爪付きナットが手持ちに有ったのでそれを使う予定だ。
写真 爪付きナットを埋め込む予定
設計では爪付きナットの四つの爪が入り込む小穴をΦ4.5ネジ穴の周囲に四つ設けていた。
上写真では分かりにくいが、3Dプリントされた上写真のパーツにもその小穴(縦2x横1x深2)が綺麗に四つ開いている。やはり光造形法は微細な加工が可能なのだ。
ただし、爪付きナットの爪は加工精度がそんなには高く無いので、ワテの設計した四つの小穴に爪が上手く入り込まない箇所がある。
無理やり捻じ込むとレジン製のパーツが破損する可能性もあるので、爪付きナットを加熱してレジンに圧入するなどを検討中だ。
下写真はプリント基板固定用の二種類の台座にM4ボルトを通してみた様子だ。
写真 Fusion360の設計通りに高精度に印刷されているパーツ
上写真のようにピッタリとボルトが貫通している。
塩ビ管に穴開け加工を行う
さて、ここまでの調査でPCBWayさんから送られて来た3Dプリントパーツはワテの設計ミスもなく、いい感じに仕上がっている事が分った。
次は塩ビパイプに穴開け加工だ。
スピーカー固定用に四つのネジ穴を開ける
まず、スピーカー固定台座を塩ビパイプにしっかりとテープで固定しておく(下写真)。
写真 スピーカー固定台座をVU150塩ビパイプにしっかりとテープで固定して穴を開ける
上写真のように一つ目のドリル穴を開けた。
3Dプリントパーツのネジ穴がドリルガイドとなるので、真っ直ぐに塩ビ管にドリル穴を開ける事が出来た。
塩ビパイプなので、鉄工用ドリルで簡単にΦ4の穴が開いた。
穴が貫通したら、下写真のようにボルトを通して位置ずれしないようにして、二個目、三個目と穴を開けて行った。
写真 パーツがずれないようにボルトを通しながら穴開け作業を行う
スピーカー取り付け位置に大穴を開ける
さて、今回のVU150の塩ビパイプ加工で最大の難関である大穴を開ける作業だ。
FOSTEX P1000K付属の説明書によると、バッフル板にはΦ94の穴を開けるように指示されている。
どんな道具を使ってΦ94の穴を塩ビ管に開けるか?難しい問題だ。
本当ならΦ95mmのホールソーが有れば一発で開けられる。
そんなホールソーは持っていないし、わざわざ買うのも勿体ない。
そこで道具箱を探したら、金工用の自由錐(サークルカッター)を発見した。
写真 まずは金工用の自由錐で塩ビパイプの穴開けに挑戦
ただしワテが持っている自由錐は最大でΦ76mmまでしか開けられない。
まあ、それでも良いので試しに開けてみた(下写真)。
写真 鉄工用自在錐で穴開け加工に挑戦したが硬くて上手く行かない
その結果、上写真のように塩ビパイプ表面を少しは削る事が出来たのだが、これ以上深く削るのは危険なので中止した。
ここまでの作業で分ったのは、塩ビパイプが丸くて不安定なので作業がやり辛い。
何らかの手段でしっかりと塩ビパイプを固定して、自由錐もボール盤に取り付けて真っ直ぐに塩ビパイプに切り込めば安定して穴開けが出来たかもしれない。
でも現実は塩ビパイプを体で押さえながら下写真のドリルを手に持って穴を開けるので、不安定で危なっかしいのだ。
写真 自由錐の穴開けに使ったデウォルト(DEWALT)製電動ドリルドライバー(AC100V改造済)
ちなみにこのデウォルト(DEWALT)製電動ドリルドライバーは四極スピコンを使ってAC100V駆動に改造している(下写真)。
写真 四極スピコンを使ってAC100V駆動に改造したDEWALT製充電式電動ドリルドライバー
ホールソーを使う
次に試したのが金工用のホールソーだ。
写真 超硬ホールソーΦ32で穴開けしてみる
ワテが使ったホールソーはボッシュの製品では無いが、以前どこかのリサイクル屋で安かったので買っていたやつだ。
その結果、下写真のようにΦ32の穴を開ける事が出来た。
写真 塩ビパイプVU150(厚さ5.1mm)の中心にΦ32を開けた
ただし、下写真のように切り取った円盤状の塩ビパイプ破片がホールソーの中に嵌ってしまい、取り除くのに苦労した。
写真 切り取った塩ビパイプ破片がホールソーの中に食い込んだので引っ張り出した
上写真のホールソーはホール部分の深さが短いので厚い部材の穴開けには適していないようだ。元々、鉄板やステンレスの薄板用のホールソーだし。
ホールソーは押したり引いたりしながら開けると良い
そこでワテの工具箱を漁ったら、以前に購入していた別の金工用のホールソーを発見。
写真 Φ25とΦ24のホールソーを発見
この赤色のホールソーはΦ24なので、確かキャノンコネクタをアルミパネルに取り付ける時に穴開けする用途に買った記憶がある。
そのホールソーを使うと下写真のようにサクサクと簡単にΦ24穴を開ける事が出来た。
写真 深型ホールソーΦ24を使って六個の穴を開けた塩ビパイプ
この場合も切り取った円盤状の破片がホールソーの内部に食い込んでしまうと取り除くのが困難だ。
実は一つ目の穴開けで食い込んでしまった。そうなると六角レンチで中心のドリル刃を外して円筒内部に食い込んでいる塩ビ破片を取り除く必要がある。非常に面倒な作業だ。
つまり、一気にホールソーを押し込んで穴を開けようとすると再び塩ビ円盤破片がホールソー内部に食い込んでしまう。
そこで二個目の穴を開ける時には、ホールソーを押したり引いたりしながら少しずつ削って行くような感じで作業したら、貫通した時に塩ビ円盤破片がホールソーに食い込む事無く穴開けする事が出来た。
そんな調子で合計六個のΦ24穴を開けたのだ。
DIY作業では掃除が重要
ここで床に大量に飛び散っている塩ビ破片を掃除する。
写真 ワテ自作のサイクロン集塵システムを使って床の塩ビ切り屑を吸引清掃
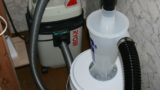
金工用ノコギリを使って塩ビパイプをくり抜く
さて、下写真のダイソーで100円で買った鉄工用ノコギリを使って塩ビパイプをくり抜く事にした。
写真 ダイソーで買った100円の金切りノコギリ
その結果、下写真のように切り取る事が出来た。
写真 ダイソーの100円の金切りノコギリもまあまあ使える
さて、この金切り鋸を使って上写真の黒いマジック線に沿ってクルッと一周に渡って円形に切り取るのは難しい。
塩ビパイプの穴開け加工にはジグソーが最適だった
そこでジグソーを使ってみる。
念のために白い養生テープを貼って、ジグソーには木工用の曲線切用の刃を付けて塩ビパイプを切ってみた。
写真 ジグソーを使うと塩ビパイプは綺麗にカット出来る
その結果、上写真のようにサクサクと塩ビパイプを切断する事が出来たのだ。
最初からジグソーを使えば良かったわ。
自称DIY達人のワテであるが、こんな大口径の塩ビパイプの加工は初めての経験だ。
で、下写真のように二個目の塩ビパイプはΦ24のホールソーで二箇所に穴を開けておいた。
写真 二個目の塩ビパイプはΦ24のホールソーで二箇所に穴を開けておく
そして下写真のようにジグソーを使って切り取って行く。
写真 ホールソーで開けたΦ24穴からジグソーで切り始める
その結果、下写真のように簡単にΦ94の大穴を開ける事が出来たのだ。
写真 ジグソーを使うと簡単にΦ94mm穴を開ける事が出来た
ジグソーで切った切断面は滑らかではないので、金工用の半円形のヤスリで切断面を削ってならしておいた。
あとは下写真のようにカッター刃の背中のエッジを使って塩ビパイプの角を削った。
写真 カッター刃の背中のエッジを使って塩ビパイプの角を削る
無事にスピーカー取り付け穴Φ94を開ける事が出来たので、下写真のようにスピーカー固定台座で塩ビパイプを挟んで六角穴付M4x50半ネジボルト(鉄黒)を取り付けてみた。
写真 スピーカー固定台座で塩ビパイプを挟んで六角穴付ボルトで仮固定
上写真のようにいい感じでピッタリと組み上げる事が出来た。
なお、今回は四つの固定穴に四本のM4ボルトを通して、FOSTEXスピーカーと白い固定台座を一緒に塩ビパイプに固定する予定なのだが、スピーカー固定と台座固定は別々のボルトでやるほうが良かったかも知れない。
つまり、上写真の四カ所のボルトはスピーカー固定専用とする。
なので、上写真にあと二箇所か四カ所くらいのネジ穴を開けて、塩ビパイプを挟み込んでいる白い台座を固定するのだ(スピーカーは固定しない)。
そして、台座が固定出来たら、そのあとで上写真の四つのネジ穴を使ってスピーカーを固定する。
まあそのやり方のほうが組み立てや分解がやり易いだろう。
どうするかな。
まあ何なら白い台座は塩ビパイプに接着剤で貼り付けてしまっても良い。
そうすれば上写真の四本のボルトはスピーカー固定に使える。
どうするかは組み立て時に考えよう。
スピーカーターミナル固定台座用の穴開け加工
次はスピーカーターミナル固定台座の穴開け加工だ。
スピーカー台座の穴開け加工と同じく、下写真のように台座をテープでしっかりと固定した。
写真 スピーカーターミナル固定台座の穴開け加工(テープでしっかり固定)
そして下写真のようにΦ4の鉄工用ドリル刃で穴開け加工する。
写真 スピーカーターミナル固定台座の穴開け加工(Φ4鉄工ドリルで穴開け)
なお、スピーカー台座やスピーカーターミナル台座の取り付け用のボルト穴は塩ビパイプにΦ4の鉄工ドリルで開けたが、その後、Φ5に広げておいた。
下写真のように中央部にΦ25の穴をホールソーで開けた。
写真 鉄工ドリルやホールソーの切り口がささくれている
塩ビパイプはドリルで穴開けすると切断面がスパッとは仕上がらずに、ささくれ立つ。
そこで下写真のコニカルドリルを使ってザグリ加工する。
写真 コニカルドリルを使ってザグリ加工
このコニカルドリルは一本持っていると穴開け加工する時にザグリ加工が簡単に出来るのでお勧めだ。アルミ板のバリを削る取る事も出来る。
下写真のようにコニカルドリルを使ってザグリ加工すると、ドリル穴のささくれたエッジを綺麗に出来る。。
写真 ターミナル取り付け穴にコニカルドリルでザグリ加工中
下写真のように綺麗にザグリ加工が出来た。
写真 穴開け加工、ザグリ加工が完了したターミナル取り付け穴
下写真のスピーカー固定穴もコニカルドリルでザグリ加工しておいた。
写真 穴開け加工、ザグリ加工が完了したスピーカー取り付け穴
と言う事で、無事に塩ビパイプの穴開け加工が完了した。
なお、塩ビパイプはVU150x500mmなのだが、スピーカーの取り付け高さはワテが椅子に座った時の耳の高さより数センチくらい下げている。
その理由は、最終的にはこの塩ビパイプに何らかの底板を取り付けて安定させるので、数センチくらい高くなる可能性もある。
もしスピーカー位置が耳の高さよりも高いと底板を付ければ益々高くなるが、予め低めにしてあれば高くする事は可能だ。
そう言う理由でスピーカー取り付け高さを決めている。
まとめ

ワレコ
塩ビパイプの穴開け加工は初めての経験だった。
穴開け加工には自在錐、ホールソー、金切り鋸、ジグソーなど使ったが、結局はジグソーが最も適していた。
当記事ではワテが自作中の塩ビ管を利用したスピーカーに使う3Dプリントパーツの紹介と塩ビ管の穴開け加工の詳細を説明した。
3Dプリントパーツは今回PCBWayさんに3Dプリンタの光造形法によるレジン素材での印刷を依頼して作成した。
光造形法による印刷物は噂通り、高精度に仕上がっていて、非常に満足感の高い仕上がりになっている。
それらの3Dプリントパーツを使って、塩ビ管に穴開け加工を施した。
塩ビ管と言う曲面素材の表面にネジ穴を開ける作業では、PCBWay製の3Dプリントパーツを当てがってネジ穴位置を決めて、それをドリルガイドとして使う事が出来たので、非常に精度良く穴開けが出来た。
一方、塩ビ管にΦ94mmのスピーカー取り付け穴を開ける作業では、自在錐、ホールソーなど試したが最もやり易かったのはジグソーだった。
今後の予定としては、以下の作業を予定している。
- 塩ビパイプの塗装
- スピーカーターミナル用のプリント基板にスピコン、バナナプラグターミナルなど半田付け
- スピーカーの取り付けと配線作業
- 塩ビパイプの底板、天板を作成(木材を使う予定)
- ワテのPCオーディオ環境に塩ビ管スピーカーを組み込み
などだ。
近日中に完成させたい。
(続く)
コメント